Here is what you will find in this edition:
- Ask Doctor SIS: “The Price of Business”, by Angela Summers
- “Why Bad Things Happen to Good People”, by Bill Mostia
- “SIS Management (part 4) – Bypass Management”, by Eloise Roche
- Unsafe Automation, incident cases
- New Alarm Management Training Course, by Mike Carter
- SIS-TECH Application Case, by Pete Fuller
- SIS-TECH Workshop Series (new)
- Follow SIS-TECH on technical events and training calender
Ask Doctor SIS
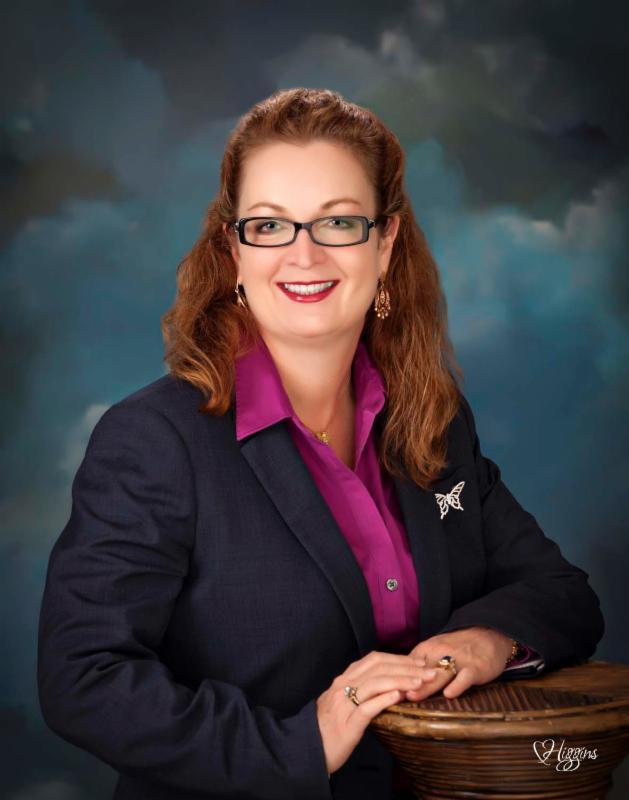
Angela E. Summers Ph.D., P.E.
One of the biggest challenges to safe operation is the availability of highly competent instrumentation, controls and electrical services for turnaround testing and quality assurance. Once equipment is installed and operational, the use of individual suppliers to support revalidation efforts is impractical and ineffective. No supplier has expertise with their competitor’s products so troubleshooting the installation can turn into endless finger pointing and little resolution. SIS-TECH designs new and upgraded installations every day and has deep expertise with many types of specialized equipment. We understand how the overall integrated system works and know the tricks and hidden features that yield optimum performance from instrumentation, controls, and electrical systems.
SIS-TECH can plan, coordinate, execute, record, and QA/QC your critical installations, whether in safety controls, alarms, interlocks, safety instrumented system, or equipment protection applications. Dr Summers was recently featured on the Price of Business with Kevin Price discussing these services and how a temp-to-perm model is being used to guarantee a pool of qualified personnel.
Click here to have full access to the interview
Why Bad Things Happen to Good People?
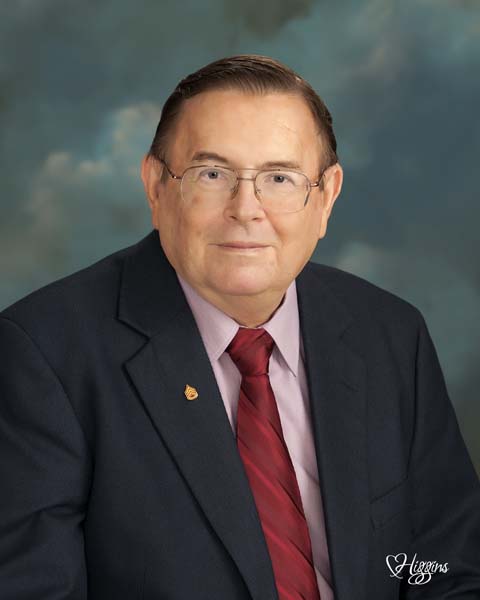
William L. Mostia P.E.
Accidents in the process industries are extensively investigated to determine root causes, for lessons learned, and many times in search of the “guilty”. Accidents are seldom simple and most accidents have human elements that led to or facilitated the accident. Many times the people involved in these accidents, when considered individually on their merit, would be considered “good” people yet “bad things” (accidents) still occur.
Introduction to SIS Management Part 4: Bypass Management
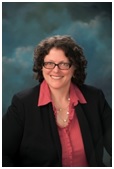
Eloise Roche, Senior SCAI Consultant, CFSE
A bypass called by any other name is just as dangerous. Whether referred to as an inhibit, suppression, or forcing, the bypass of a safety system device or automated function nearly always means that this safeguard will no longer be able to provide the full degree of risk reduction and reliability it was specified to perform. Continued safe operation of that facility will usually depend on timely implementation of compensating measures to provide the risk reduction that was lost through the act of bypassing.
The predictable consequences of bypassing a safety instrumented system device or function lead to the following dual requirements for bypass management:
- Features to prevent and alert unauthorized use (and other operator error)
- Highly effective management of change and access security controls.
Please visit this edition’s Unsafe Automation Incident case study, to see an example of how failure in safety interlock bypass management led to a multiple fatality outcome.
Bypass Management Unsafe Automation Incident
Our next industry incident case study showcases how the lack of safety interlock bypass access restriction led to a vapor cloud explosion. Unfortunately, this unsafe automation practice, which had persisted despite multiple PHA and near-miss incident recommendations to the contrary, was compounded on this day with a less than adequate evacuation response to area release monitors, resulting in multiple fatalities. This incident occurred at a polyvinyl chloride facility located in Illiopolis, Illinois, April 23, 2004.
Read more about the Illiopolis incident here.
SIS-TECH New Alarm Management Training Course
Control Systems Engineer and Senior Consultant, Mike Carter, teaches our new Alarm Management class. Mike has over 30 years of control engineering experience in refining, chemicals, energy, manufacturing, and applied research organizations. He held roles as a contributor and technical lead in engineering, plant, joint venture, and development positions. Emphasis in recent years has been on safety instrumented systems and alarm management.
Mike is a long-term member of the ISA18.2 alarm management standard committee, a contributor to TR4 (Enhanced and Advanced Alarm Methods) and TR7 (Alarm Management when Utilizing Packaged Systems), and is a member of the ISA84 safety instrumented system standard committee.
Opening training class was February 2-3, 2016 and the feedback couldn’t be better!
“One of the most valuable courses I have attended”, Mr. Jared Witte, from Kuraray
SIS-TECH Application News!
SIS-TECH was contacted by an end-user who was within weeks of starting a major turnaround. The project design team needed to find a quick solution to address a hazardous event that had been recently identified during a detailed process hazards analysis. The design team needed a SIS, because excess hydrocarbons in the waste gas feed could result in an internal detonation with possible injury of the operator due to direct contact with flammable materials or the shrapnel produced during loss of containment.
The design team specified 3 gas analyzers in the waste gas line to detect high hydrocarbon concentration. The gas analyzers reported the % LEL (Lower Explosive Limit), and when the % LEL exceeded the setpoint the SIS took action on 3 valves to stop the waste gas feed. The logic solver voted the gas analyzers 2oo3 to achieve high safety integrity and reliability. The implementation of this safety function accomplished the objective of the process hazards analysis recommendation. Additionally, an examination of common in-service failure modes of the analyzers indicated that leaving an analyzer in calibration mode was highly likely since the analyzers required frequent calibration. The analyzers also had potential failures that could be detected by internal diagnostics that initiated a fault alarm to notify the user that the analyzer was no longer tracking the process condition. The safety logic was expanded to account for these failure modes, so that during on-line operation either an analyzer fault alarm or switching to calibration mode served as a vote to trip for each analyzer channel.
In summary, the Diamond-SIS tripped the waste gas valves based on a 2oo3 vote of the waste gas analyzers. A vote to trip could be initiated by % LEL, detected fault, or detected calibration mode. The trip and fault detection strategy was easily implemented using a Diamond-SIS, which was built, tested, and shipped in just 6 weeks. Again, the fastest delivery and most cost-effective solution was provided by the Diamond-SIS.
What is SIS-TECH up to?
SIS-TECH Workshops:
SIS-TECH will be holding the first of a series of workshops and an open house on March 31, 2016 at our headquarters in Houston, TX.
If you would like to attend, please contact Mandy Dixon at mdixon@sis-tech.com.
Events:
SIS-TECH was at the 71st Instrumentation & Automation Symposium
12th Global Congress on Process Safety & 2016 AICHE Spring Meeting
April 10-14, 2016
Houston – GRB
AFPM 2016 Reliability & Maintenance Conference
May 24-27, 2016
San Antonio – Henry B. Gonzalez Convention Center
29th Annual Environmental Health & Safety Seminar
June 6-9, 2016
Galveston – Moody Gardens Convention Center
Training:
Mar. 9, 2016, Process Hazard Analysis (PHA) – 2 day course in fundamentals of the Process Hazard Analysis. Class outline
Mar. 22, 2016, SIS Implementation -3 day course in an overview of the SIS management system – the Safety Lifecycle. Certification of completion from MKOPSC. An optional test may be taken to become PRISM-Certified. Class outline
Apr. 12, 2016, Layers of Protection Analysis – 2 day course in fundamentals of Layers of Protection Analysis (LOPA). Class outline
May 3, 2016, SIL Verification Using Quantitative Techniques – 2 day course in verification of safety instrumented functions. Class outline
May 5, 2016, SIL Solver – 1 day course using SIL Solver Software; a SIL verification tool. Class outline